Made in China, Intelligent Manufacturing
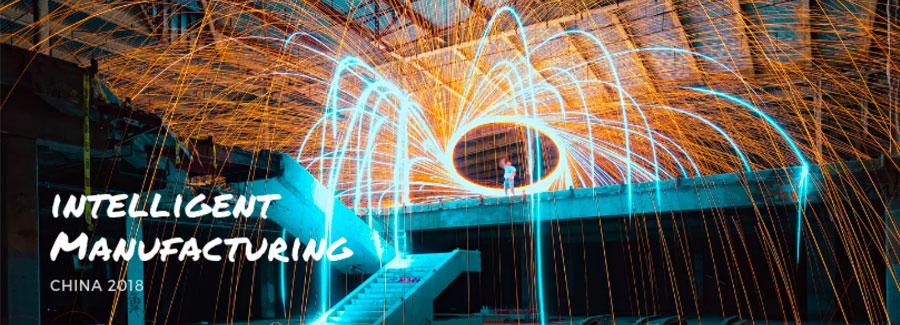
The hottest topic in China's manufacturing is intelligent manufacturing. The Chinese government also vigorously supports manufacturers to promote intelligent manufacturing through various policies and funds.
Enterprises with the demand and strength in various industries are itching to try, hoping to reduce manpower, cut costs, flexibly respond to market changes, better meet customer needs and improve business competitiveness by promoting intelligent manufacturing. With the introduction of the Internet of Things and services, manufacturing will soon build a global network in the form of CPS (cyber physical systems), integrating equipment, warehousing and production facilities.
The core of the “upgraded version” of industrial manufacturing is to connect the information flow through informatization and digitalization, create a lower-cost, higher-performance, more flexible manufacturing capacity and realize intelligent manufacturing.
Generally, the production and operations management process of an enterprise can be divided into planning, execution and control levels.
Using management systems (ERP, MRP, etc.) at the planning level, an enterprise can integrate its existing production resources and work out production plans according to the customer demand, inventory and market forecast; the execution level formulates workshop operation plans according to the production plans issued by the planning level, arranges processing tasks at the control level, summarizes and reports the execution of the operation plans and tasks. The whole production process in the factory is not transparent. When there are changes to the production plans, material shortages, equipment failures, processing quality problems and so on, if information cannot be effectively transmitted, production cannot be timely adjusted and optimized.
To fill the information gap between the planning level and the control level, MES at the control level came into being. MES monitors production information in real time. It passes information up to the planning level and controls the execution level, connecting the enterprise’s upper production planning systems with the lower equipment control systems in the workshop. It fills the gap between the upper level and the lower level and opens the factory’s information channel, which makes it the basis and necessary condition to realize the “upgraded version” of industrial manufacturing.
MES (manufacturing execution systems) is a set of production information management systems for manufacturing enterprises. MES can provide enterprises with manufacturing data management, project schedule management, production schedule management, inventory management, quality management, human resources management, work and equipment management, tool and uniform management, procurement management, cost management, Kanban management, production process control, underlying data integration and analysis, upper data integration and decomposition and other management modules, creating a solid, reliable and feasible collaborative manufacturing management platform for enterprises.
MES was first proposed by American company AMR in the 1990s, aiming to strengthen the executive function of MRP and link MRP with the shop floor control system (SFCS) through the execution system. Here, the shop floor includes PLC, data collectors, barcodes, various measuring and testing instruments, manipulators, etc. MES is designed with necessary interfaces for the factory to establish cooperative management with the manufacturers that provide the shop floor control facilities. As new technologies such as cloud computing, mobile terminals and big data are integrated into industrial automation, manufacturing is moving from informatization to intelligent manufacturing. Intelligent manufacturing has to integrate and analyze fragmented and scattered data by MES, and link up the enterprise’s product design, customer management, supply chain management and efficiency management systems through data connectivity, to realize the overall optimization of the bottom control level, middle execution level and upper planning level. Finally, it will make manufacturing enterprises’ use of assets more efficient, production costs lower and market risks controllable, thereby improving the overall competitiveness of manufacturing.
MES is part of enterprise informatization. It was first proposed by AMR in the United States. Then it developed rapidly in the United States and Europe. The future market space for MES software is vast. Its compound growth rate has remained around 40%. In 2014, the global market size for MES was about 41.6 billion Yuan. In the past five years, the market size has maintained an average annual growth rate of 21.65%. By 2020, the market size for MES is expected to reach 93.1 billion Yuan. It will maintain a compound annual growth rate of 18% in the future.
The demand for MES in China is huge. In 2014, the market size for MES was about 2.6 billion Yuan in China, up 25% year on year. The market size is expected to reach 10 billion Yuan by 2018. In the future, the average growth rate will remain around 40%. Moreover, the growth rate of the Chinese MES market is significantly higher than that of the international market. This benefits from the large-scale industrial reform toward automation in China.
MES is mainly used in two kinds of industrial manufacturing: continuous manufacturing and discrete manufacturing. Continuous manufacturing includes petroleum and petrochemical, chemical, metallurgy and mining, pharmaceutical, food, beverage and other industries concerning people’s livelihood. Discrete manufacturing includes automobile, machinery manufacturing and electronic communication industries.
MES is widely applied to continuous manufacturing. In 2013, the application of MES in petroleum, petrochemical and chemical industries was already mature, because of their high degree of automation and informatization, production process development and early application of MES. The potential demand for MES in metallurgy and mining was weak because of their excess production capacity and slowing growth. The potential demand for MES grew fast in pharmaceutical, food, beverage and other industries concerning people’s livelihood, because of their high downstream demand.
The application level of MES is low in discrete manufacturing. In the past, discrete manufacturing used ERP or MRP for enterprise management. Manufacturing costs were lower back then, so they could guarantee higher gross profit levels for enterprises. Enterprises paid little attention to middle management between the upper level and the lower level. However, with the soaring HR cost, land cost and environmental cost, market competition has become increasingly fierce. Since the total environment has changed dramatically, flexible production was put forward in for discrete manufacturing. In 2013, the increasingly intensified competition in the Chinese automobile market required MES to cover vehicle manufacturers and auto parts manufacturers from top to bottom. With the implementation of various macro policies and the acceleration of infrastructure construction, machinery manufacturing hit bottom and rebounded, so the demand for MES grew steadily. The labor-intensive electronic communication industry, which mainly involves assembly, has high requirements for assembly line speed and quality and attaches importance to material supply, product traceability and technical KPI. In this industry, MES is widely used. With the steady growth of the consumer electronics industry, the application of MES in this industry also has rapid growth.
With the changes in domestic and international economic environment, the demand for informatization and digitalization has been increasing in China’s manufacturing. Enterprises now pay more attention to lean production and flexible manufacturing. The demand for MES at the middle execution level also has fast growth. Compared with overseas, China has a relatively short history of developing MES. The market is just emerging. By drawing on the development models of advanced foreign MES manufacturers and according to the demand of equipment manufacturers, Chinese enterprises develop MES suitable for Chinese manufacturing. MES has been industrialized in developed countries and a number of leading enterprises have emerged. Chinese MES enterprises are small in scale and weak in competitiveness at present. Due to the low MES usage rate in Chinese manufacturing, the market is more flexible. Moreover, the cost of Chinese software talents is relatively low and software service enterprises have a better understanding of manufacturing processes. As a result, China will soon have a group of outstanding MES enterprises.
In addition, the idea of industry 4.0 has swept the world in recent years. It will be the direction for China's manufacturing transformation and upgrading. The core of industry 4.0 is to connect the information flow through informatization and digitization, and realize information interaction between upper, middle and lower levels, to achieve intelligent manufacturing. Industrial software exists in every corner of intelligent manufacturing. Important industrial software includes MES, PLM (PDM), etc. MES is the key to intelligent manufacturing. It is the intersection of all steps (production, engineering and manufacturing). As an important part of manufacturing enterprise informatization, MES has a broad prospect for application in the era of "industry 4.0".
China is a large manufacturer in the world. Thanks to the rapid development of manufacturing in recent years and the increasing input into informatization and digitalization, MES will have great potential for wide application in China. It will maintain a steady and fast growth for the foreseeable future.